C2 PROJECT
C2 Photo Album
album:February 2017 working party
Injector bodies, with the outsides nicely cleaned up by Chris.
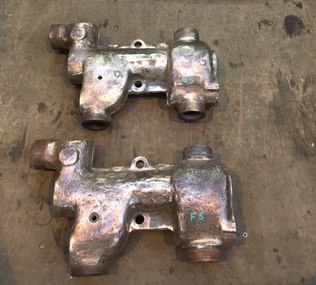
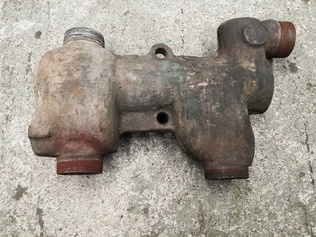
The injector bodies were in this condition before Chris started work. It's been suggested that these look like a Mayan dog sculpture
Chris ready for action!
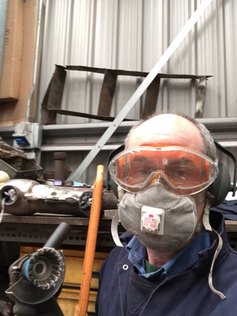
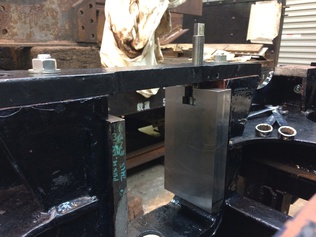
Wedge faceplate, adjuster bolt and horn keep successfully assembled into the loco frame. The axlebox should fit in the gap between them. The size of the gap can be fine-tuned by turning the wedge bolt to move the wedge faceplate up and down. The bolt is then locked in place with a locknut (not shown).
Axleboxes machined and with thrust faces assembled. We need a smaller countersink to do the last holes in the renewable thrust faces - a job for 2 weeks time. Not too much more to do on these now.
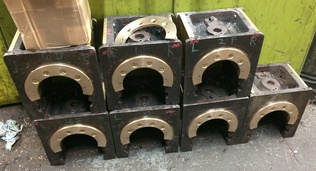
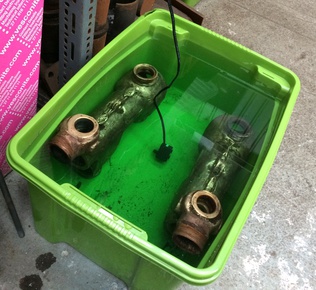
The injector bodies in a bath of citric acid, to remove scale from the insides. That's a tiny circulation pump in there with them.
Re-tapping the wedge bolt holes in the horn keeps, using the big DSG lathe. This took a while to set up but it worked well.
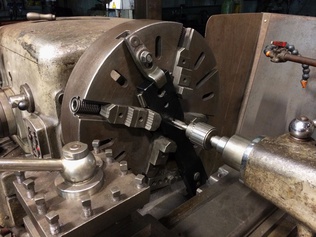

All 8 Axleboxes with oil grooves freshly machined in the brass wear plates. - Andrew Nelms 18/02/2017
An axle journal bearing with a 'lead in' ground into the bronze. This helps the bearing pick up the oil off the oil pad and draw it into a film on the bearing surface. - Andrew Nelms 18/02/2017
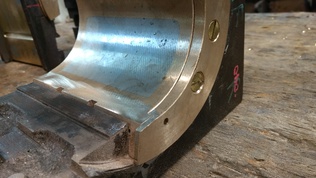
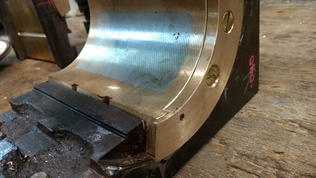
The Journal bearings as machined by Martin. - Andrew Nelms 18/02/2017
Machining the oil grooves in the axlebox brass wear plates. - Andrew Nelms 18/02/2017
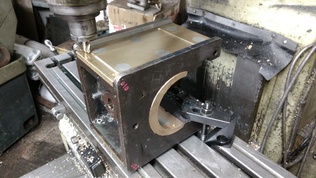
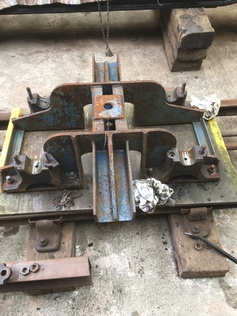
It seems a long time since Paul built this skate for shifting the loco across the cob. Here the blue skate is upside-down with the wheels out. - Chris Barry 20/02/2017
Julian welds a new section onto the bolster of the red skate, ready to support the loco frames. The new boiler for 'Welsh Pony' is visible in the background. - Chris Barry 20/02/2017
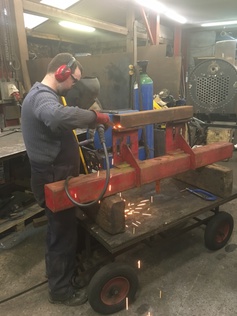
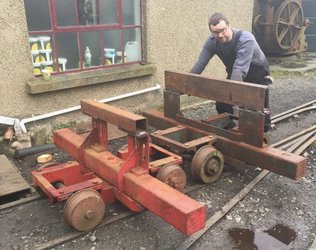
The skates are not quite as shiny as they once were, but they're ready for their next task. Julian pushes the skates back to the C2 shed. - Chris Barry 20/02/2017
Moving a hole sideways by 6mm: the plug has been pressed in and welded (on the other side) and is now ready for tapping.
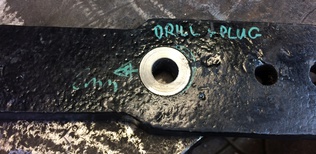
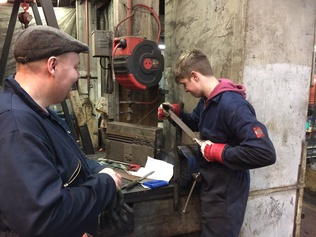
Will and Matt prepare the brake retaining straps.
Dave 2 cuts some tube to length ready for assembly of the temporary drawbar.
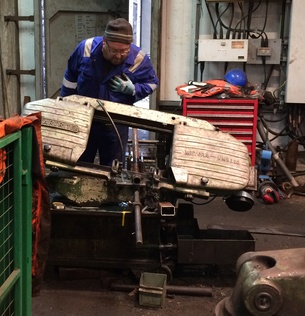
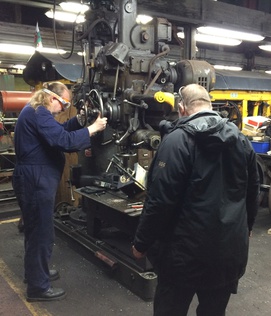
Dave 1 and Colin machining oil holes in the axleboxes using the Asquith radial arm drill.
A closeup of the axlebox being drilled.
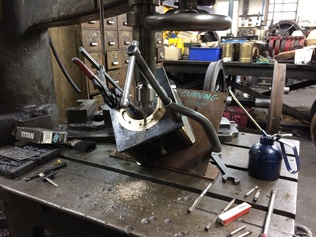
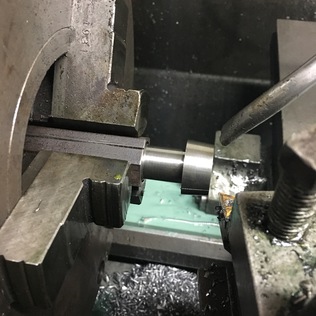
Alan's setup for skimming the tapered faces of the wedge adjuster bolts. This was necessary to achieve the desired travel down the wedge face.
Dave, Alan and Paul assemble the horn keeps and wedge bolts onto the frames to check fit and clearances
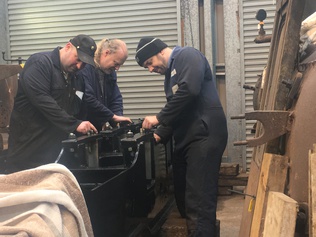
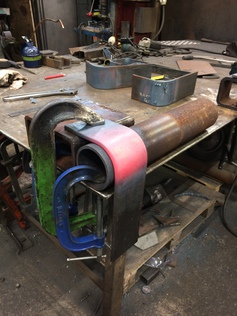
The end result - a neat curve to the correct radius.
Trial assembly of horn keep and wedge bolt.

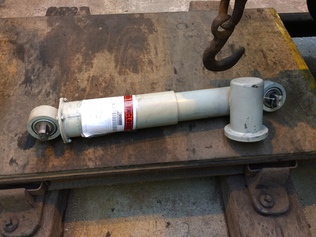
The large yaw damper for our loco/tender drawbar. This is of a type used on many main-line trains and was kindly supplied by Unipart Rail.
A row of axleboxes in the paint shop, ready for finishing. The one without the oil grooves is the ninth (spare) box and we have left some additional material on this which can be machined to suit if/when it is needed in future.
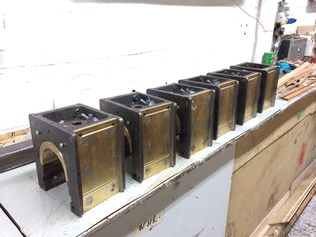
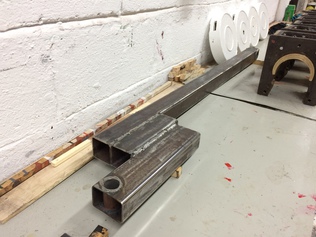
The temporary drawbar. This is a lightweight fabrication for shunting within the yard only. It will fit at either end of the loco or tender, and will enable us to move the frames around prior to finishing the proper drawgear. In future it will also be useful if we wish to shunt the loco and tender separately.
The six strips which retain the brake gear on axles 2, 3 and 4.
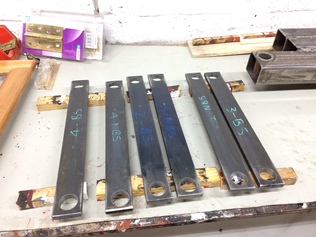
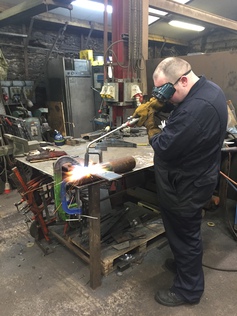
Paul uses the oxy-propane torch to heat up some strip ready for forming it.
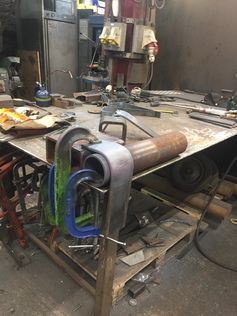
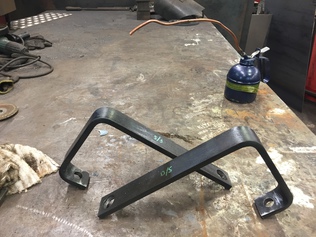
The brake retaining strips for axle 1 are a more complicated shape which was hot-formed from strip. Matt made these with a little guidance from Paul.
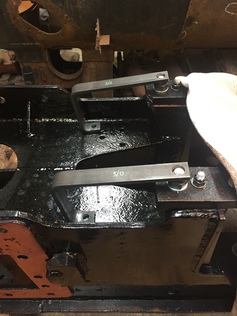